Wed
01
Jun
2022
Industry Update
Hi all
Just a note to let you know about what’s going on in the industry. Currently as you know we have pricing going up and inventory levels going down. We are driven by the petroleum market and are feeling the increases. Also manufactures are feeling the increasing problem of getting and keeping materials in stock.
Gratefully, we have been fortunate that we have several manufactures to get material from. We have seen some material shortages, but our inventory and abilities to shop several manufacturers has been helpful in aiding our customers and finding comparable products when necessary.
One piece of advice is to call as soon as you can if there is something you need. If its on backorder we need to get you inline for when it is replenished with the manufacturer. We also have been increasing several areas of our inventory to compensate for the market shortages.
Give us a call or email to get your order in!
Mon
19
Nov
2018
Craft Vinyl Sheets
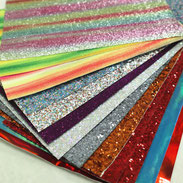
Well it took us long enough!! Lol But, finally, we have a FULL line of pre-sheeted craft vinyls. We literally have brought in over 100 colors, patterns, holographic, and glitters. We have noticed the need to service the craft industry.
We have modified a section of our warehouse and added individual sections to house all of the Craft Vinyls.
These materials are all first run product. What's that mean? well, most of the online materials are seconds or end cuts off of rolls. These aren't. They are taken directly off of master rolls.
Everything is listed on the site, under products - craft vinyl.
As always, just give us a call with any questions or concerns!
Fri
29
May
2015
Heat Press Material Problems
From time to time we get calls that heat press material isn’t sticking to the garment. There can be several factors at play. We will discuss a few and hopefully they will answer some basic questions.
- More pressure. The material is called HEAT PRESS for a reason. Most of the time more pressure in the press will resolve the problem. Most of the lines call for medium-firm pressure. I like to error more on the firm side. Occasionally a additional pressing of the garment is required, or a minor adjustment of heat.
- Heat. When dealing with the heat aspect, you should get a digital thermometer and verify that the platen is at the desired temperature. Occasionally the heat presses are off a few degrees and that may affect your final product. Also be sure to check if you have an imported press, mostly they are in Celsius not Fahrenheit.
- Different materials. Thermoflex Plus will work on cotton, polyester, knits, and blends. When dealing with moisture wick materials there are a few additional steps needed. Most of the moisture wick shirts have a coating on them that deters the garment material from sticking. Pre-washing the garment helps, wiping the garment with alcohol and then pressing out the moisture is probably the best step to prepare it for the transfer.
As always we are here to help. Feel free to call us, you will speak to a person, not an automated phone system.
Wed
06
May
2015
Use ThermoFlex to create a faux rhinestone look
Want to create a better rhinestone look for garments? Well its easier than ever. Just look over the attached PDF and order some of the ThermoFlex Glitter Flex Ultra and you are in
business. There are several advantages:
- Material feels natural (nothing projecting from the garment)
- You can out faux Rhinestones on the back of garments
- Longer Life
- More color selections
- Faux Rhinestones can be cut into shapes (hearts, clovers, ect...)
These are just a few of the ideas......let your creativity take over!
Feel free to comment with any questions.
Mon
04
May
2015
The Plotter Blades we sell
Ok, today I was asked about the plotter blades that we sell and why they were so less expensive than the blades from the manufacturer. Well as to the price........I really don't have an
answer why ours average $15 per blade and the manufacturer direct blades average in the $60 range. But what I can tell you is that our blades are first ground, meaning that they are not
re-manufactured, our our made from new high carbon steel. We have been selling the blades from the same manufacturer for over 20 years. Our blades have a long life associated with
them as well as a good price point. We have blades for all makes and models of plotters. Trust me they are good blades at a great price. Give them a try...you will not be
disappointed.
Wed
29
Apr
2015
Glitter Flex ULTRA *New Colors
Specialty Materials has added some new colors to their Glitter Flex Ultra Line.
- Creates Stunning Results with 64 colors to choose from
- REAL glitter flakes encased in high quality heat sealing adhesive
- Great for adding value and making your designs stand out
- Pressure sensitive carrier enables easy weeding and repositioning.
Application Instructions:
- 60° blade
- Cut the material in a mirror image
- 330°F - 335°F
- Firm, even pressure
- 17-20 seconds
- Peel warm, use Teflon sheet and repress for 2 seconds
- Wash inside out, wash cool, tumble dry
Our customers have been successful in using this material for a variety of projects. It can also be used to mimic rhinestone's, and you can cut them into various shapes such as hearts
with the added benefit of having a smooth finish on the garment when done. As always if there are any questions please feel free to call us of leave a comment.
Mon
27
Apr
2015
What is Mottling?
Vinyl surface issues (rough, dull or mottled)
• Mottling or a dull finish is common among highly pliable and conformable cast
and calendered vinyl. The surface of the film can appear to be slightly dull as
the liner leaves minor embossing.
Mottling usually occurs when a roll of graphic film is wound too tightly or
stored at a high humidity. It is not a surface defect and will disappear
within a few days of installation. To remove mottling prior to cutting or
printing, release the tension of the roll for a few days by loosening the tape
used to fasten the end of the roll. Applying light heat with a heat gun will also
remove mottling.
• Thermal printing on mottled film could create an undesired printing effect. For
optimal results, use the suggestions above to remove mottling prior to thermal
printing.
Special Considerations and Uses
Mottling is a special consideration for vinyl films. Mottle looks like a haze, or blotchy
dull spots on the vinyl film surface. This condition occurs when the glossy top surface
of soft, conformable vinyl film is pressed against the release liner in a wound roll.
While conform-ability is a benefit of vinyl films, it also makes them prone to mottling.
Factors affecting the level and severity of mottle include heat, time wound in a roll,
roll tightness, film formulation, and liner type. Also, film color and gloss level have an
effect. Mottle will show up more on higher gloss films and darker colors.
(TIP) To prevent mottle, store vinyl films in a cool area, away from direct sunlight or a
heat source. Rolls should be wound as loosely as possible and suspended or kept in
boxes with end plugs. Laying rolls on their sides can produce a "band" of mottle.
(TIP) Mottle can be reversed. To eliminate mottle, unroll the vinyl and leave it lying in
a warm area. Or, carefully use a heat gun (or hand-held hair dryer) over the film
surface. The mottle should begin to disappear. Once film is applied to a substrate,
most mottle will eventually disappear with time and exposure to heat or sunlight.
Wed
22
Apr
2015
Magnetic Sheeting Care and Use
Here are a few tips on how to use magnetic sheeting, specifically for vehicle applications
Do vehicles need special preparation before applying magnetic signs?
Make sure that the pain is perfectly clean, dry and waked where the signs are to be placed. Also make sure that the back of the sign is clean and clear of
debris.
What is the best way to apply a magnetic sign?
Let one edge of the sign contact the vehicle in the desired position. Let the magnetic power do the works as it puts the sign into place from the edge where you started to the edge of
the opposite side. if the sign is not exactly where you would like it. Peel it off and repeat the steps above. Make sure that the entire sign is smooth and free of air pockets.
During the winter the temperature of the sign should be approx. 50 degrees during instillation, the vehicle temperature does not matter.
What surfaces present problems?
Care should be taken with wood grain paneling and metallic finishes. Such surfaces should be checked weekly. A generous application of wax should be applied to both the sign and
the vehicle. DO NOT place signs on freshly painted surfaces.
What sign maintenance is recommended?
Remove the sign weekly, cleaning and wiping dry both the sign and the vehicle. keep the sign free of dirt and debris. remove and clean after rain and snow.
What special precautions must be taken when storing magnetic signs?
Avoid wrinkling by storing in a 3 inch diameter roll with the printed side out. or store flat avoiding stress on the signs and curling.
Additional Tips:
DO NOT wash the vehicle with the signs in place.
Check and clean both surfaces weekly.
Corner rounding prevents "dog eared" corners
Please remember that the manufacturer WILL NOT accept and responsibility for damage to a vehicle. Please follow these steps and let you customers know the proper way to care for them.
Hope this helps alittle.........
Mon
20
Apr
2015
The difference between Cast and Calendered Vinyl.
Let's begin with a few of the basics on vinyl films. Most vinyl
films are made from the same basic raw materials. We begin
with polyvinylchloride (PVC) polymer, which is simply basic
plastic, and is, by nature, relatively rigid. Other ingredients
are then added to the PVC. These ingredients include:
plasticizers to make the film flexible, pigment to make the
desired color, and additives to help achieve specific
properties such as UV absorbers to improve resistance to
UV radiation, heat stabilizers, fillers and processing aids.
These raw materials can be chosen from a wide range of
quality levels. Of course, for a film with limited durability,
often the least expensive raw materials are chosen.
Apart from the type of raw materials that are used at
manufacturing, the manufacturing process and the type of
plasticizers used create the main differences of vinyl films.
Vinyl films can either be made by calendering or by casting.
Each of these processes renders different qualities of films.
Casting generally results in better quality films. The grade of
plasticizers that is used to make the film flexible also greatly
affects the grade of the film. Generally for pressure-sensitive
adhesive films a choice is made between polymeric and
monomeric plasticizers. We won't go into detail on the
plasticizers in this article, but for simplicity's sake consider
polymeric to be the higher grade and monomeric to be the
economy grade plasticizers. The combination of these factors
greatly determines the durability of vinyl films.
Cast Films
Cast films, also known in the
industry as premium, high performance
or 2 mil are
considered to be a premium product with excellent durability
and conform-ability characteristics. The term "cast" refers to
the manufacturing process of this type of vinyl. Making a
cast vinyl film is a lot like baking a cake. The vinyl begins
with a "recipe" calling for a list of ingredients known as the
formulation. These materials are added to a "bowl" or mixing
churn in a predetermined order while mixing at specific
speed and for a set amount of time to ensure a complete
and consistent mixture. This liquid mixture, known as
organosol, is then "poured" or cast onto a moving web
known as the casting sheet and is then processed through a
series of ovens which allows for the evaporation of solvents.
When the solvents are evaporated, a solid "film" is left
behind. The film is then wound up in large-diameter rolls for
subsequent adhesive coating. The casting sheet determines
the texture of the film.
Because the vinyl is cast on the casting sheet in a relaxed
state, this material offers very good dimensional stability.
This process also allows the film to be very thin (most cast
films are 2 mil), which helps with the conform-ability of the
product. Material manufacturers recommend the use of cast
films on substrates such as fleets, vehicles, recreational
vehicles or boats where the customer wants a "paint-like"
finish that will last a long time, usually five to eight years
depending on how the film is processed.
Advantages of cast films:
• Shrinkage is the lowest of all vinyl films because the
"casting sheet," not the film itself, is pulled through the
machine. Since the film has not had any stress applied
during the manufacturing process it does not try to
resume or shrink back to its original form.
• Durability of cast films is generally higher than that of
other vinyl films due to the manufacturing method and
the raw materials used.
• Cast films can be made very thin which produces a
conformable product that allows application over
substrates with rivets, corrugations, and complex
curves. Also, once applied, this low caliper makes the
graphic less vulnerable to abrasive forces.
• Cast films also maintain their color and other properties
better than other vinyl films. This results in better
performance of pigments and UV absorbers.
• The manufacturing process of cast films makes it easy
to run small productions of special colors to match. It is
relatively easy to change color during production
making color matching in small batches possible.
Calendered Films
Like cast, calendered film also
gets its name from the
manufacturing process. These
films may also be referred to
as intermediate, 4 mil, short term
or economy. Calendered
vinyl is formulated with similar
raw materials as cast, except
that no solvents are used. The
batch is mixed and heated to a molten state that resembles
pizza dough. Once the film reaches this molten state it is
extruded through a die and is then fed through a series of
calendering rolls. These polished steel rolls progressively
squeeze and stretch the vinyl into a flat sheet (similar to
flattening out dough with a rolling pin). Because the film is
stretched into shape, it has some degree of memory and
therefore is less dimensionally stable than cast vinyl films.
This means that when a calendered film is exposed to heat
the film will have a tendency to shrink or pull back towards
its original form. Calendered films also tend to be thicker
(usually 3.2 to 3.4 mils) than cast films because of the
limitations of the calendering process. Unlike casting where
a textured or smooth casting sheet is used to produce the
film finish, calendering implements a special finish cylinder at
the end of the process while the film is still warm. This
process is extremely fast and is ideal for bulk production
runs. Therefore, color matching is very unattractive on these
machines. However, due to its bulk production with high
yields, calendered films are relatively inexpensive.
The quality of calendered films can range from economy to
intermediate with durability of one to five years. These films
generally are not recommended for vehicle applications
because they are thicker, less conformable and less durable
than cast films.
Advantages of calendered films:
• Greater production yields equals less cost
• Stiffer/thicker film equals easier handling
• Thickness of film increases resistance to abrasion
As with anything else, the finished product is only as good as
what you put into it. This begins with choosing the right vinyl
for the job. If you are doing a full vehicle wrap where you
want the graphic to conform so that it looks and performs
similar to paint you should choose a material with these
characteristics, which would be cast film. Calendered films
are ideal for applications that do not require the film to
stretch or conform around contours. Examples of calendered
film uses would be floor graphics, wall murals, and point-of purchase
displays.